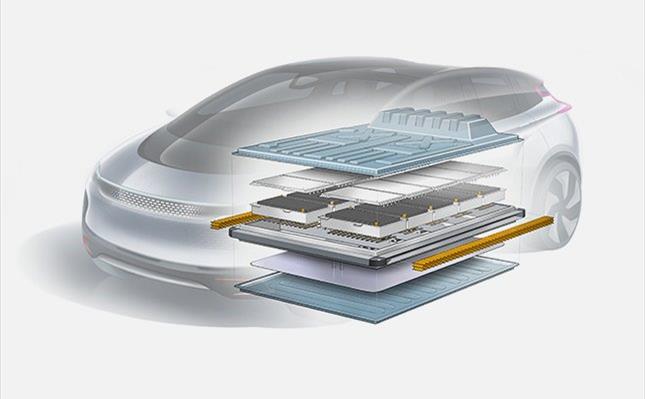
EV Batteries
Demands for greater electric vehicle (EV) range and efficiency have focused attention on improving battery packs. To address challenges that include better thermal management for longer life, lighter weight to extend vehicle range, greater energy density, and simplification of complex designs and assembly processes, the industry is turning to thermoplastics
Multi-material thermoplastic solutions for battery packs can deliver better thermal performance, part integration for lighter weight and cost reduction; higher energy density for improved efficiency; electrical isolation and thermal insulation for safety; and opportunities to increase sustainability.
SABIC offers a full range of materials for battery packs, including short and long glass fiber-reinforced polypropylene (PP) with non-halogenated flame retardance, and high-temperature engineered thermoplastics.
BLUEHERO™ ELECTRIFICATION INITIATIVE
SABIC has elevated its focus on solutions for EV batteries through BLUEHERO – a strategic initiative design to help accelerate the world’s energy transition to electric power and support meeting global goals on climate change.
Through BLUEHERO, SABIC has built an expanding ecosystem of materials, solutions and expertise to help the automotive industry create better, safer and more efficient EVs.
Learn more.

Featured Product Brands
Ask us about solutions for EV batteries.
Covers, lids, trays and enclosures
By replacing traditional materials such as aluminum with thermoplastics in battery enclosures, lids and covers, manufacturers can reduce weight significantly. Designers can create complex geometries such as deep draws and streamline configurations by potentially eliminating the need for ceramics and mica sheets used with metal for thermal runaway protection, or by integrating cooling channels with battery trays. Molding supports high-volume production and helps avoid the costly secondary operations needed for metal. In addition, recyclable thermoplastics can provide a more sustainable solution than metal.

Featured Product Grades
PP homopolymer; 15% glass fiber reinforcement; high flow, halogen-free flame retardance; UL94V0@3mm rating. |
|
PP homopolymer; 25% glass fiber reinforcement; high flow, halogen-free flame retardance; UL94V0@1.5mm and 5VA@3.0mm flame rating. |
|
PP homopolymer; 30% glass fiber reinforcement; high flow, halogen-free flame retardance; UL94V0@1.5mm and 5VA@3.0mm flame rating. |
|
PP copolymer; 30% glass fiber reinforcement; high flow, halogen-free flame retardance; designated injection molding grade for electrical applications. |
Module boxes and lids
Key trends affecting battery modules include raising battery cell energy density and creating slimmer battery packs to provide greater freedom in vehicle design. Using high-performance thermoplastics in module boxes can enable part integration for weight savings and thin-wall designs to free up space for more cells or a smaller module footprint. These materials also contribute to safety through thermal and electrical isolation of the modules to prevent propagation.
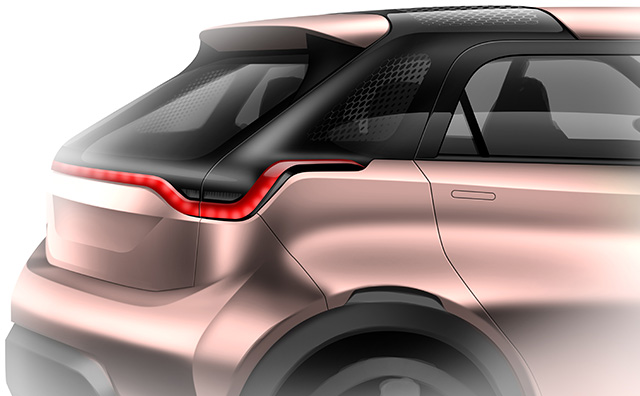
Featured Product Grades
PP homopolymer; 15% glass fiber reinforcement; high flow, halogen-free flame retardance; UL94V0@3mm rating. |
|
PP homopolymer; 25% glass fiber reinforcement; high flow, halogen-free flame retardance; UL94V0@1.5mm and 5VA@3.0mm flame rating. |
|
PP homopolymer; 30% glass fiber reinforcement; high flow, halogen-free flame retardance; UL94V0@1.5mm and 5VA@3.0mm flame rating. |
|
PP copolymer; 30% glass fiber reinforcement; high flow, halogen-free flame retardance; designated injection molding grade for electrical applications. |
|
PC resin; unfilled; good flow and release; non-halogenated flame retardance; UL94 V0 rating; injection molding grade. |
Battery onboard charger
Optimizing the on-board charger (OBC), which manages the flow of electricity from the grid to the battery, includes minimizing its size and weight and increasing efficiency. Replacing incumbent metal with non-conductive, flame-retardant thermoplastics can address these challenges. Thermoplastics are lighter than metal, enable part consolidation and new designs, and protect against corrosion.
Featured Product Grades
General purpose PBT resin; 30% glass fiber reinforced; injection molding grade; flame retardant; UL94V0@0.71mm and 5VA@2.0mm flame rating; UL746C f1 listed. |
Side frame reinforcement
Protecting lithium-ion batteries from crash energy caused by side impacts requires effective reinforcement. Energy-absorbing XENOY™ HTX resins used for side frame components can protect battery cells and are compatible with e-coating. When compared to metal, thermoplastic crash absorbers give more flexibility in designing parts such as innovative honeycomb structures that conserve space, lower costs and deliver a high ratio of impact absorption to weight.

Featured Product Grades
XENOY™ HTX950 |
Polyester-based alloy; unfilled; high temperature resistance; low temperature ductility; high energy absorption; e-coat compatibility. |
Polyester-based alloy; 30% high strength glass fiber reinforcement; excellent strength, stiffness and heat resistance; e-coat compatibility. |
|
Polyester-based alloy; 35% high strength glass fiber reinforcement; excellent strength, stiffness and heat resistance; higher modulus; e-coat compatibility. |
|
PBT/PC alloy; unfilled; excellent low temperature impact and chemical resistance; gray, black colors. |
|
PC/PBT blend; unfilled; impact modifier; solvent resistance; low temperature ductility. |
Battery cell separators
Placing separators in battery modules can help prevent or slow down thermal runaway and fire propagation. These polymer films with microscopic pores physically isolate the anode and the cathode while allowing ions to circulate between them. The heat that is generated during thermal runaway melts the pores, so they close, shutting out the heat from the adjacent battery before it ignites. Requirements include extreme thinness and high heat resistance. Polycarbonates surpass ceramics and mica sheets, which are heavier and more expensive.
Featured Product Grades
PC resin; unfilled; good flow and release; non-halogenated flame retardance; UL94 V0 rating; injection molding grade. |
|
PP copolymer; 30% glass fiber reinforcement; high flow, halogen-free flame retardance; designated injection molding grade for electrical applications. |