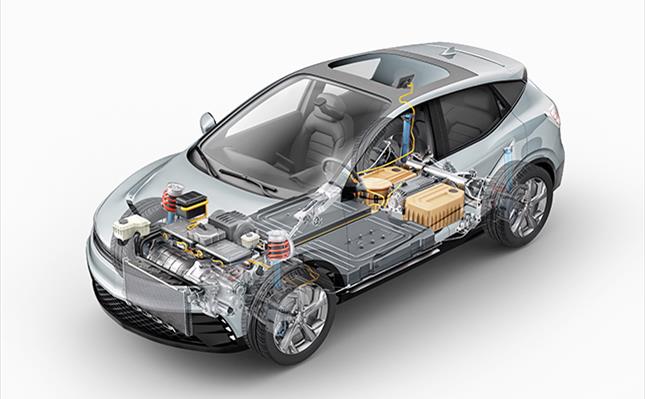
Under the Hood
The electrification megatrend is influencing under-the-hood components. For example, EVs and hybrids are prompting the shift from mechanically to electrically driven oil pumps. Electric motors and power converters in EVs, which emit electromagnetic energy, require EMI/RFI shielding to avoid crosstalk that can cause malfunctions and failures.
At the same time, OEMs continue to focus on classic challenges such as weight and mass reduction and extended useful life, even though these issues may have different implications for EVs vs. conventional vehicles. While EVs already have a weight advantage under the hood due to their small electric motor (and other parts) vs. a large, heavy internal combustion engine, they still benefit from lighter materials to extend vehicle range, optimize performance and free up space for more electronics. EV manufacturers are replacing metal with lighter thermoplastics in under-the-hood parts or using them in hybrid plastic/metal structures. Thermoplastics also enable part consolidation, simplified designs and thin-wall components that can help reduce system costs.
For both EVs and conventional vehicles, the under-the-hood environment is harsh. Parts must withstand exposure to chemicals and high heat without deforming or warping. As more sensors, such as thermal monitoring, battery impact detection and pressure sensors are added, they require protection from electromagnetic fields and radio signals. SABIC’s specialized thermoplastics, including ULTEM™ resins and LNP™ compounds, can help protect components to maximize their useful life.
A quiet ride is a hallmark of EVs. However, noise and vibration caused by under-the-hood parts can be a problem in conventional vehicles. Materials like LNP™ LUBRILOY™ compounds that integrate lubricants can help minimize noise and vibration from plastic parts.
Furthermore, as in other areas of the vehicle, OEMs seek sustainable materials to advance their environmental goals. SABIC’s upcycled ELCRIN™ iQ resin and bio-based ULTEM™ resin grades support circularity.
Featured Product Brands
LNP™ Compounds |
Specialty compounds delivering targeted properties like heat dissipation, EMI shielding, lubricity, dimensional stability and RF absorption, while supporting customers’ sustainability goals through recycled, upcycled and bio-based formulations. Of particular note, our LNP™ STAT-KON™ compounds can provide anti-static or static dissipation performance for fuel line clips, in-line filter housings, fuel filter brackets and pockets, inlet control valve bodies and poppets. |
NORYL™ Resins |
Modified polyphenylene ether (PPE) resins featuring high stiffness and strength and good hydrolytic, chemical and creep resistance. |
NORYL GTX™ Resins |
PPE resins with polyamide offering dimensional stability, low density and good hydrolytic, chemical, temperature and creep resistance. |
ULTEM™ Resins |
PEI resins known for exceptional heat resistance, high precision tolerances, metallization and plating capabilities, high strength and stiffness and broad chemical resistance. |
ELCRIN™ iQ Resins |
PBT resins that are chemically upcycled from PET bottles to help achieve circularity goals. |
Cylinder Deactivation Valves
Many ICE and hybrid vehicles are equipped with eco driving modes to conserve fuel and increase sustainability. When this mode is selected, the valve deactivates two or three cylinders, depending on the car. ULTEM™ resin is well suited for molding cylinder deactivation valves, thanks to its dimensional stability, low coefficient of thermal expansion, high-temperature resistance and exceptional durability over millions of cycles. Bio-based grades of ULTEM resin are also available.
Featured Product Families
ULTEM™ Resins |
are PEI materials featuring dimensional stability, high-precision tolerances, metallization and plating capabilities, heat resistance up to 217°C, IR transparency and resistance to harsh environments. |
Sensors
Under-the-hood sensors are proliferating, especially in EVs. They collect data on critical metrics, such as oil pressure and glycol pressure, detect battery impact, and monitor thermal conditions, lubrication levels and battery performance. ULTEM™, NORYL™ and NORYL GTX™ resins and LNP™ compounds (e.g., LNP KONDUIT™ and LNP FARADEX™ compounds) can deliver properties such as high-heat performance, chemical resistance, thermal conductivity, EMI shielding and dimensional stability for sensor housings, internal layers and quick port connectors.
Featured Product Families
NORYL GTX™ Resins |
are PPE resins with polyamide offering dimensional stability, low density, and good hydrolytic, chemical, temperature and creep resistance for potential use in ignition coils, junction boxes and connectors. |
NORYL™ Resins |
are low-density PPE materials featuring high stiffness and strength and good hydrolytic, chemical and creep resistance. |
ULTEM™ Resins |
are PEI materials featuring dimensional stability, high-precision tolerances, metallization and plating capabilities, heat resistance up to 217°C, IR transparency and resistance to harsh environments. |
LNP™ FARADEX™ Compounds |
provide inherent EMI/RFI attenuation using electrically conductive stainless-steel fibers. Potential applications include sensor and electronic control unit (ECU) housings and windshield-mounted toll boxes. |
LNP™ KONDUIT™ Compounds |
are thermally conductive compounds that transfer heat into a heat sink or the surrounding air to help extend product life. They are well-suited for applications requiring thermal management, such as battery modules and sensor components. |
Oil Pumps
Electric and hybrid vehicles are incompatible with mechanically driven oil pumps because if the engine stops, the cooling loop ceases. This situation has caused a shift to electrically driven pumps that continue supplying oil even when the engine is shut off (such as by idling stop systems). However, electrically driven pumps cannot withstand temperatures higher than 85°C, when soldering points begin to melt. Furthermore, as these pumps are integrated into the e-axle of EVs, the coefficient of thermal expansion will become more critical. SABIC’s ULTEM™ resins can potentially replace metal in pump components to reduce weight while delivering strength, thermal resistance and dimensional stability. When ULTEM resin is used with internally lubricated LNP™ LUBRICOMP™ compounds, pump operations may be enhanced with lower friction and reduced noise-vibration-harshness.
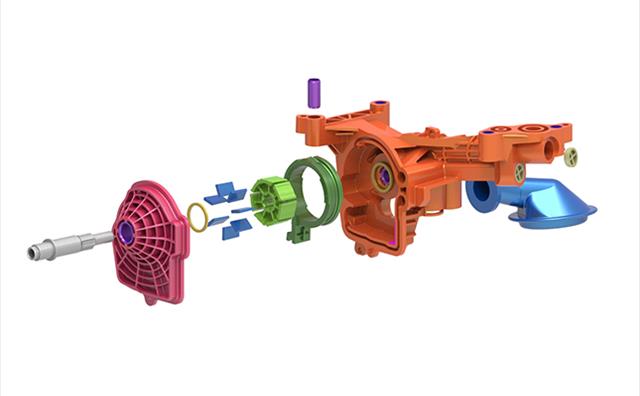
Featured Product Families
ULTEM™ Resins |
are PEI materials featuring dimensional stability, high-precision tolerances, metallization and plating capabilities, heat resistance up to 217°C, IR transparency and resistance to harsh environments. |
LNP™ LUBRICOMP™ Compounds |
are based on PC/ABS or PPE resins and incorporate either silicone or PTFE lubricants. |
LNP™ KONDUIT™ Compounds |
are thermally conductive compounds that transfer heat into a heat sink or the surrounding air to help extend product life. They are well-suited for applications requiring thermal management, such as battery modules and sensor components. |
Connectors
Connectors are critical EV applications that require stability over time and in various environments. Connector materials should deliver electrical insulation and isolation, and heat resistance. With the evolution of EVs with higher voltages, up to 800V, flame retardance is a focal point. Also, the implementation of the DC fast-charging infrastructure with higher temperatures is increasing the need for materials with effective thermal management.
Featured Product Families
LNP™ ELCRIN™ iQ Resins |
are chemically resistant PBT materials that are upcycled from discarded PET water bottles to help support sustainability goals. |
ULTEM™ Resins |
are PEI materials featuring dimensional stability, high-precision tolerances, metalization and plating capabilities, heat resistance up to 217°C, IR transparency and resistance to harsh environments. |
NORYL™ Resins |
are low-density PPE materials featuring high stiffness and strength, and good hydrolytic, chemical and creep resistance for potential use in connectors, Ignition coils and junction boxes. |
LNP™ KONDUIT™ Compounds |
are thermally conductive compounds that transfer heat into a heat sink or the surrounding air to help extend product life. They are well-suited for applications requiring thermal management, such as battery modules and sensor components |
Water Pumps
Under-the-hood water pumps circulate ethylene glycol to cool electronics below 80°C and protect from fluids. Many pump housings are made with die-cast aluminum. Replacing metal with SABIC’s ULTEM™ or NORYL™ resins or LNP™ KONDUIT™ compounds can support greater design freedom without sacrificing high-heat performance or chemical resistance.
Featured Product Families
ULTEM™ Resins |
are PEI materials featuring dimensional stability, high-precision tolerances, metalization and plating capabilities, heat resistance up to 217°C, IR transparency and resistance to harsh environments. |
NORYL™ Resins |
are low-density PPE resins featuring high stiffness and strength and good hydrolytic, chemical and creep resistance. |
LNP™ KONDUIT™ Compounds |
are thermally conductive compounds that transfer heat into a heat sink or the surrounding air to help extend product life. They are candidates for applications requiring thermal management, such as battery modules and sensor components. |