RISK AND EMERGENCY RESPONSE AND CRISIS MANAGEMENT
PROCESS RISK MANAGEMENT AND RISK DISCOVERY AND MANAGEMENT
As part of SABIC’s 2025 EHSS strategy, we focused on sustaining the mindset of welcome Risk Discovery through smart KPIs that encourage reporting risks while equally advocating adequate risk response to permanently mitigate them through SABIC’s Assurance for EHSS Risk (SAFER) risk management and stewardship. The global implementation of the IT enabler (eSAFER), continuous monitoring, and visibility for EHSS risks were achieved along with active IT enabler enhancements to facilitate stewardship for EHSS risks. In 2022, these included:
– A Dust Hazard Analysis (DHA) task pilot conducted in the MEA region, along with training at sites that handle explosive dusts. Since several sites handle explosive dust, DHA aims to ensure adequate understanding and assessment to avoid dust-related explosions and fires.
– PRM’s development of an LOPC evaluation tool that was incorporated in SABIC OMS to support consistent classification of process safety events and drive informed decisions.
– Sponsoring regional process safety conferences and active participation in the GPCA’s newly formed process safety network, reflecting SABIC’s responsible care outlook.
– The development of SABIC SHEM 3 operating and maintenance procedures, including a transformation journey and an updating of current standards, is undergoing a SABIC Global review with 45 participants, and will be followed by a function stakeholder review.
– Improving progress on SHEMs including developing and revising technical guidelines, such as PHA, Transient Operation HazOp (TOH), Layer of Protection Analysis (LOPA), Bowtie, the SAFER Without Further Risk Reduction (SWFRR) process, and Cost Benefit Analysis (CBA) Guidelines.
– Supporting many corporate root cause analyses (for example: steam cracker furnace tube failure, asset question root causes analysis, etc.).
EMERGENCY PREPAREDNESS AND RESPONSE CAPABILITIES
The SABIC Emergency Response and Fire Protection (ER&FP) function focused its efforts on monitoring emergency-response KPIs through EHSS maturity and support sites to overcome challenges to ensure effective response and readiness for emergencies. ER& FP launched an emergency-response application for quick reference of resource availability and healthiness, and developed mandatory competency programs and trainings for emergency-response teams globally, such as NFPA 1072- HAZMAT and Certified Fire Professional Specialist (CFPS).
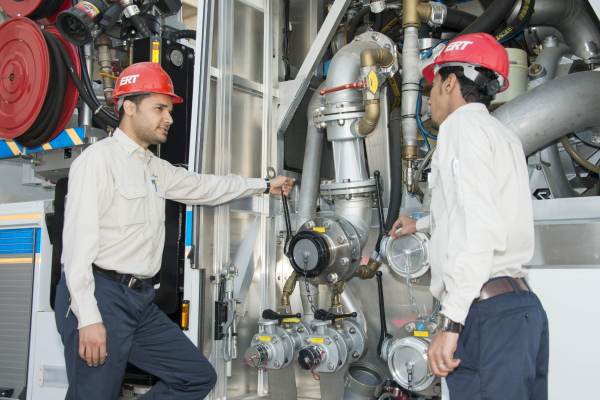
We monitor emergency response KPIs to ensure effective response and readiness for emergencies
PROCESS-RISK ASSURANCE
In line with MFG 2025 EHSS strategy, PRM focused on Risk Discovery and Management Capabilities, incorporating the improvements of SAFER structures and work processes. The Process Safety Maturity Index was developed to improve visibility and remedies to those areas of focus, as well as findings from the assessments cycle done on the EHSS management system. To assure process-safety element performance and compliance:
– SABIC conducted several audits related to PS elements under I-MEA, such as Hadeed, Gas, Sabtank, Yanpet, etc.
– We initiated a PS SHEM elements committee network that meets on a quarterly basis.
– We updated the process safety competency development program for frontline staff in alignment with WFD-OMS 131.
– SABIC continuously responded to SHEMs system clarifications from end-users and updated the process safety standard glossary.
GLOBAL CRISIS MANAGEMENT
While regional and local crisis management teams continue to respond to the COVID-19 pandemic and climate-related emergencies, cybersecurity has become a priority concern as an ongoing threat to the industry, as a cyber-attack can have a major negative impact on manufacturing operations. SABIC is committed to ensuring its crisis management teams receive continuous training, including conducting exercises, and continuing to review and update crisis management plans. This year, SABIC’s cybersecurity response team partnered with the regional Security and Crisis Management teams to conduct 15 site-based and region-wide exercises. These exercises challenged the teams with their responses to cyber-attacks.
In addition, SABIC initiated the third phase of the Crisis Management Mobile Application, a communication and announcement tool used by all crisis teams globally. Scope and blue prints were finalized in Q4 2022, and go-live is planned for Q1 2023. The biggest challenge in 2023 lies in the process of successfully incorporating and synchronizing all SABIC businesses with the Crisis Management Mobile Application.
ENVIRONMENTAL STRATEGY
As a Responsible Care® company, we are committed to making our operations as safe, stable, and compliant as possible in an effort to protect our environment and communities and conserve natural resources.
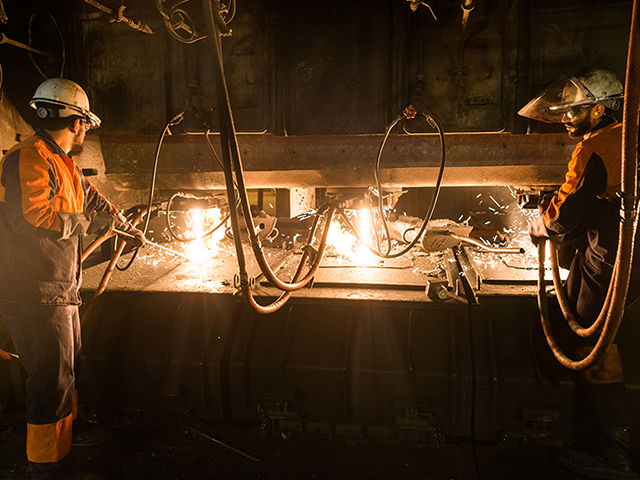
We are committed to operating our facilities in a safe, stable, and compliant manner.
ENVIRONMENTAL RELEASES AND EMISSIONS MANAGEMENT
WASTE
Realizing that sustainable waste management and transitioning toward a circular economy are vital to mitigating our environmental footprint, we applied rigorous waste-management principles, including effective and compliant waste identification, segregation, packaging, labelling, storage, and transportation. We regularly visited the external waste-management facilities to ensure that waste is properly managed. Moreover, our waste-minimization programs are focused on reducing SABIC’s footprint in waste generation. We continuously seek options to eliminate or reduce toxicity, reuse/recycle, and recover waste.
We worked on decoupling waste-related data from the material loss metric as part of SABIC's efforts to improve environmental-related disclosures and provide more information about our performance on waste generation. SABIC directed its efforts at enhancing its definition of waste in KPIs, including an internal guidance that meets the requirements in GRI 306 and provides the right granularity. The plan is aimed to start disclosing waste in accordance with GRI criteria in 2023.
WATER
SABIC constantly explores technologies to conserve natural resources and ensure minimal environmental impact from water use. Our sustainable-water initiatives include support for Access to Safe Water, Sanitation and Hygiene (WASH) and implementation of OCS - both of which are embedded in our OMS. We maintain an inventory of wastewater sources and their characteristics that includes complete drawings of the sewer systems, potable/body contact water, process water, and on-site wastewater treatment. In addition, we obtained representative samples for process quality and compliance from reliable sampling, monitoring, record keeping, and reporting processes. Moreover, SABIC has also established processes to periodically identify potential for optimizing water usage - including maximizing its reuse - by deploying SABIC Value teams, a group of technical experts, to evaluate different ideas to optimize performance, including resource usage.
Our facilities handling plastic pellets are committed to the OCS program. This year, manufacturing and supply chain leaders from SABIC in Europe came together for a special workshop on OCS. Led by EHSS and Regulatory Affairs, SABIC’s progress in moving toward Zero Pellet Loss was discussed along with some of the challenges encountered. All the attending leaders renewed their commitment on behalf of their site or function to the OCS pledge that was instated in 2014. As part of the pledge, our pellet-handling sites in Europe are committed to gaining Third Party OCS certification through the European industry audit scheme.
AIR EMISSIONS
Most of our chemical-production facilities around the world have government-specified limits for air emissions. As compliance with these limits requires specific expertise, infrastructure, and focus on complex regulations, we ensure the use of best available technique (BAT) in the design phase of any new project. Consequently, all our sites have processes in place to identify, monitor, report, and document all air emission point sources as part of our strategy. We are continuously looking for improvements and new technologies through our global T&I centers and our external partners to further reduce our carbon footprint.
We introduced a comprehensive guidance for calculation of NOx emission (the emission of nitric oxide and nitrogen dioxide) and SOx Emission (Sulphur dioxide emissions from combustion equipment and installation such as boilers, furnaces, and heaters). This reporting guidance document provides a basis to calculate NOx/SOx Emission from all significant sources within all SABIC manufacturing affiliate(s), including T&I centers globally and its reporting requirements in accordance with GRI-305-7 emission reporting disclosure.
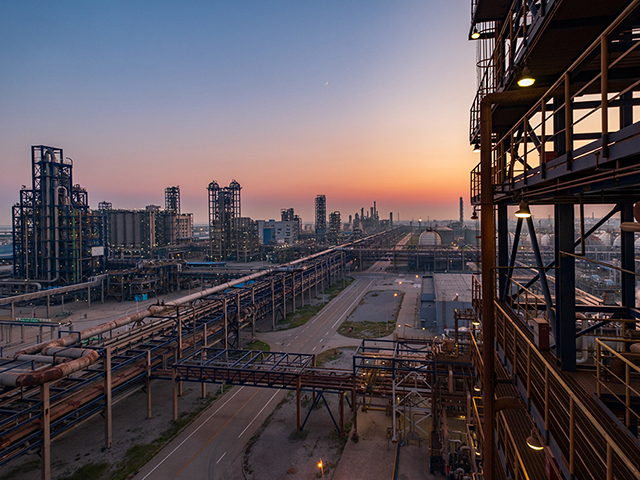
Most of our chemical-production facilities around the world have government-specified limits for air emissions.
Parameter |
|
t/year |
---|---|---|
SOx | 3,086.42 | |
NOx | 24,636.29 |
NANSHA ODOR ABATEMENT
In 2022, our Nansha plant had a scrubber +UV Oxidation+Activated carbon filter installed in addition to the existing High Efficiency Aerosol Filtration (HEAF) system to reduce its odor in air emissions. The plant completed the improvement and volatile organic compounds reduced by a further 50% while odor reduced by 70% at maximum concentrated level. The odor abatement project at Nansha is the first successful application across SABIC’s compounding sites.
BIODIVERSITY
SABIC is committed to designing and operating its facilities in an environmentally responsible manner, with a focus on reducing negative impacts on the environment and biodiversity. Our efforts to minimize these impacts include solutions that address the major drivers of biodiversity degradation in development projects, such as habitat loss and fragmentation. We prioritize the protection of biodiversity through thorough Environmental Impact Assessments (EIAs) for all our projects. EIA is is the most commonly used site-specific planning tool that evaluates the effects of a project on biodiversity, and we integrate measures for avoidance, reduction, and offsetting of these impacts into our mitigation hierarchy. Our EIAs also identify biodiversity risks, which are then integrated into the EMS at our manufacturing sites.
This year, we commenced our journey to further develop our strategy and approach toward biodiversity-related aspects in view of the need for global action on this topic. We volunteered to participate in the 2022 Global Nature Benchmark from the World Benchmarking Alliance to receive feedback on how SABIC has performed in its efforts to reduce negative impacts on nature, and contributed to the protection and restoration of ecosystems in alignment with the goals of the Global Biodiversity Framework. Our aims for 2023 include incorporating all the lessons learnt in developing our own Biodiversity Framework moving forward.
GLOBAL SECURITY MANAGEMENT
SABIC has implemented a number of security programs that focus on developing security maturity through SRAs at all our locations. We rolled out an updated SRA tool for small manufacturing sites that allows site security leaders to better identify threats to critical assets and implement appropriate risk response strategies. In addition, we conducted training awareness sessions in all regions on how to use the SRA tool.
New Security Maturity KPIs were introduced at SABIC sites that were monitored quarterly. The KPIs already included the tracking of SRA recommendations to assist leadership drive and monitor security management at SABIC manufacturing sites; now they have audit action status and security system healthiness indicators that reflect the current preparedness and functionality of the electronic security systems.
Meanwhile, SABIC continued the development of security programs and initiatives to strengthen protection, including the development of security competency (JADEER Site Security Program) for security guards in the MEA region.