SUPPLY CHAIN
SABIC’s supply chain strategy aims to deliver to customers in a timely, reliable manner, emphasizing digitalization and sustainability.
- Customer Centricity
- Innovation and Sustainability Solutions
- Product Stewardship
- Our Manufacturing Assets
- Digitalization
- Cybersecurity
- Environment, Health, Safety, and Security
- Climate Change and Resource Efficiency
- Supply Chain
- Procurement
- Raw Materials
- Our People
- Toward Saudi Vision 2030: Driving Local Content
- Communities
- Ethics, Compliance, and Human Rights
At the core of our supply chain initiatives, ultimately, are our customers―and our mission of delivering the right products, at the right time, in the right way. Offering a secure, reliable supply to our customers provides them and, in turn, SABIC, with a competitive advantage. Our fundamental aim is to establish a robust, sustainable upstream and downstream supply chain to act as local supplier in relevant markets and secure capacity for new growth.
The key supply chain activities include procurement of direct and indirect materials, and product distribution. Direct materials include raw materials directly purchased to make our products; indirect materials are all other products purchased.
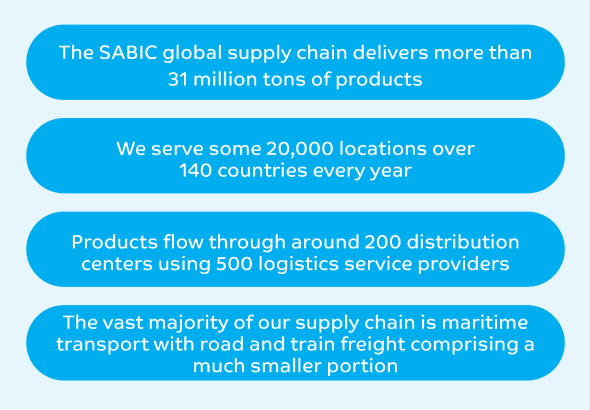
Sustainability/carbon-emission reduction targets influence the way we operate our supply chain. Taking into consideration the rapidly evolving customer expectations of sustainability, we have shifted from the lowest-cost focus to sustainable operations, thus balancing cost with customer service levels and environmental benefits. Anticipating the upcoming global regulation on shipping decarbonization, we are gradually transforming our hired chemical-tanker fleet by replacing the standard vessels with eco-designed and fuel-efficient vessels.
We are promoting and developing internal and external capabilities toward better sustainability practices along the entire value chain. Supply chain initiatives contribute to SABIC’s circular economy initiatives like TRUCIRCLETM and, thus, support the adoption of SABIC processes to use in renewable and recycled feedstock and create recyclable products and solutions for our customers.
Synergies with Saudi Aramco
Our collaboration with Saudi Aramco has contributed significantly to our success, benefitting from the latter's downstream chemicals feedstock production as well as allowing us to leverage shared synergies across procurement, supply chain, manufacturing, marketing, and sales. We are leveraging, optimizing, and expanding our facilities near Saudi Aramco processing units to reduce the need for extensive transport of products, while boosting our overall geographic presence. The integration of core processes and supply chain operations between our companies is geared toward continuous optimization of supply chain flows and operations, while jointly committing to develop infrastructure and network capabilities to foster fully integrated supply chains. SABIC and Saudi Aramco are aligning with the national agenda of Saudi Arabia in order to expand global logistics capabilities and capacities at key locations. This collaborative approach ensures that we meet customer expectations, contribute to the growth of the industry on a broader scale, and secure the future for both companies in the petrochemicals industry.
SAFETY AND QUALITY ASSESSMENT SYSTEM (SQAS)
The SQAS is a vital tool in helping the chemical industry measure logistics service providers’ (LSP) EHSS performance, assess and address gaps and areas for improvements, and identify top providers. Over the past several years, SABIC has been collaborating with other industry stakeholders, including the European Chemical Industry Council (Cefic), to develop robust criteria for sustainability assessment in the SQAS.
The SQAS assessments are valid for three years. Any service provider involved with transport or the handling of plastics must request a new assessment, which includes OCS verification by trained and accredited assessors. Reports submitted since 2022 include a reduced list of requirements, but since early 2023, it is mandatory to apply to become a SABIC logistics partner. All our service providers will have been assessed in three years, and we intend to make OCS mandatory for LSPs from the end of 2025, aiming to work only with SQAS- and OCS-certified companies.
SQAS for Total Liquids and Solids (%)
Year |
|
2023 | 2022 | 2021 | 2020 | 2019 |
---|---|---|---|---|---|---|
SQAS for total liquids | 100 | 94 | 81 | 100 | 100 | |
Target | 100 | 100 | 100 | 100 | 100 | |
SQAS for total solids | 97 | 87 | 85 | 98 | 93 | |
Target | 99 | 98 | 97 | 95 | 92 |
Read more about our supply chain priorities, including operational excellence, digitalization, and sustainability.
Disclaimer: This abridged interactive version of the SABIC Integrated Annual Report 2023 is based on the original PDF report published on this website. In case of any discrepancy, the original PDF report will prevail.