SUPPLY CHAIN
SABIC continued to leverage its global footprint and network capabilities, striving to advance resilience that upholds its competitiveness and increases customer experience in an increasingly volatile environment.
This year, the lingering COVID-19 pandemic and emerging geopolitical events have affected the global supply chain in various ways. The global shipping industry had to handle disruptions such as logistics service interruptions, decline in schedule reliability and volatile freight-rate levels. Sustaining healthy inventory levels, securing capacity and balancing customer-service levels with cost effectiveness were key aspirations for our supply chain.
Thanks to its ambitions of building a resilient network, SABIC successfully maintained its service levels to serve its customers in over 130 countries. Through the launch of the global optimization program spanning all areas of the supply chain, we leveraged our collaboration with logistics service partners and used economies of scale to sustain transportation and storage cost at competitive levels and successfully deliver 32 million metric tons of product globally.
Our global supply-chain operating model and customer-centric mindset enabled us to avoid curtailments due to the pandemic.
To combat low-schedule reliability of vessels and sustain competitive customer service levels, we inaugurated a global optimization program spanning all areas of supply chain, aiming to optimize our global network performance. Our collaboration with logistics-service partners, combined with attentive consolidation of our flows, has helped in maintaining a high level of reliability, agility and efficiencies delivering our products globally.
To further improve our Sales & Operations Planning effectiveness and value focus, drive working capital optimization and increase agility, we amplified the role of exception handling through firm criteria and governance. This helped us to be agile in our decision-making, manage disruptions, and maneuver our product flows to higher margin regions.
OPTIMIZATION AND EFFICIENCY
We capitalized on our network capabilities to optimize service levels for our customers, adopting a diversified sourcing strategy and closely collaborating with over 500 logistics service providers worldwide to secure shipping capacity and sustain cost competitiveness. In the era of localized markets and increasing competitiveness, SABIC struck partnerships and invested in collaborations, diversifying the supply base to reduce supply-side risk and take advantage of globalization efficiencies.
SABIC is aiming to leverage the rail network within Saudi Arabia and thus diversify the network-reach accessibility. Connecting the rail to our infrastructure will take us to the next level and drastically empower our logistics systems in terms of consolidating container flows and export from other ports. Rail will enable our network to connect the product flows in a more environmentally friendly manner, with reduced carbon emissions.
Digitalization is essential for deriving more end-to-end visibility and predictability, extracting actionable insights, and elevating customer experience. We continued our digital journey through our Corporate Digitization Program that covers multiple domains such as supply chain, manufacturing, market and sales, procurement, and product innovation.
We recognize that capable people and collaboration are instrumental in cultivating a dynamic organization. To this effect, we formed cross-regional and cross-functional teams to work together on a set of transformational programs (each with its own underlying governance and reporting structure) to advance network capabilities, transform sourcing strategies, and grow business.
The global supply chain is key to SABIC’s ESG governance model and Scope 3 partner engagement. This year, we continued our progress to reduce carbon emissions, in close collaboration with authorities, regulators and service provides. We use our carbon-footprint model to trace the emissions down to individual shipments and engage with our suppliers on how to make the transportation of goods more eco-friendly. Optimizing our packaging and payload, experimenting with eco-friendly technologies such as e-trucks, playing a leading role in Operation Clean Sweep and promoting the use of eco-friendly ships are some examples of our sustainability efforts.
We successfully maintained our supply-chain service levels to serve our customers
DIGITAL INITIATIVES
This year, SABIC implemented more digital initiatives into its process, as digitization continues to play an integral role in enabling faster and better operations. These initiatives include:
– Implementation of touchless orders to automate repetitive activities and improve work efficiency through seamless operations in the field of Order Management, Order Fulfilment, Documentation and Reporting.
– Continuous efforts deploying robotics process automation solutions to streamline order-to-cash work processes and increase efficiency. Scalable solutions have been developed by the broader supply-chain community to automate redundant data-entry activities and business transactions.
– The success of the Track & Trace pilot demonstrates a visibility solution that allows us to proactively respond to customers and enhance work efficiency. As a result, we have started working toward implementing it globally.
– Successfully completing the preparation phase of the AI-powered S&OP initiative, as part of our Corporate Digitalization Program, laying the foundation for better business decision-making, speed and anticipation of changes.
– Initiating the development phase of a new digital-operations platform that transforms our system landscape into a real-time connected business to complement the Corporate Digitalization Program and advance the user and customer experience.
NETWORK AND PLANNING OPTIMIZATION
SABIC achieved a major milestone in taking the lead in marketing and selling numerous Saudi Aramco affiliate’s petrochemical products. SABIC’s collaboration with Saudi Aramco and advanced integration of processes, systems and operations across the supply chain further created value for our customers.
Upscaling the high-sea model, a means of floating inventory, continued to deliver tangible benefits across the supply chain this year as high-seas delivery was deployed to transport products to further destinations and customers.
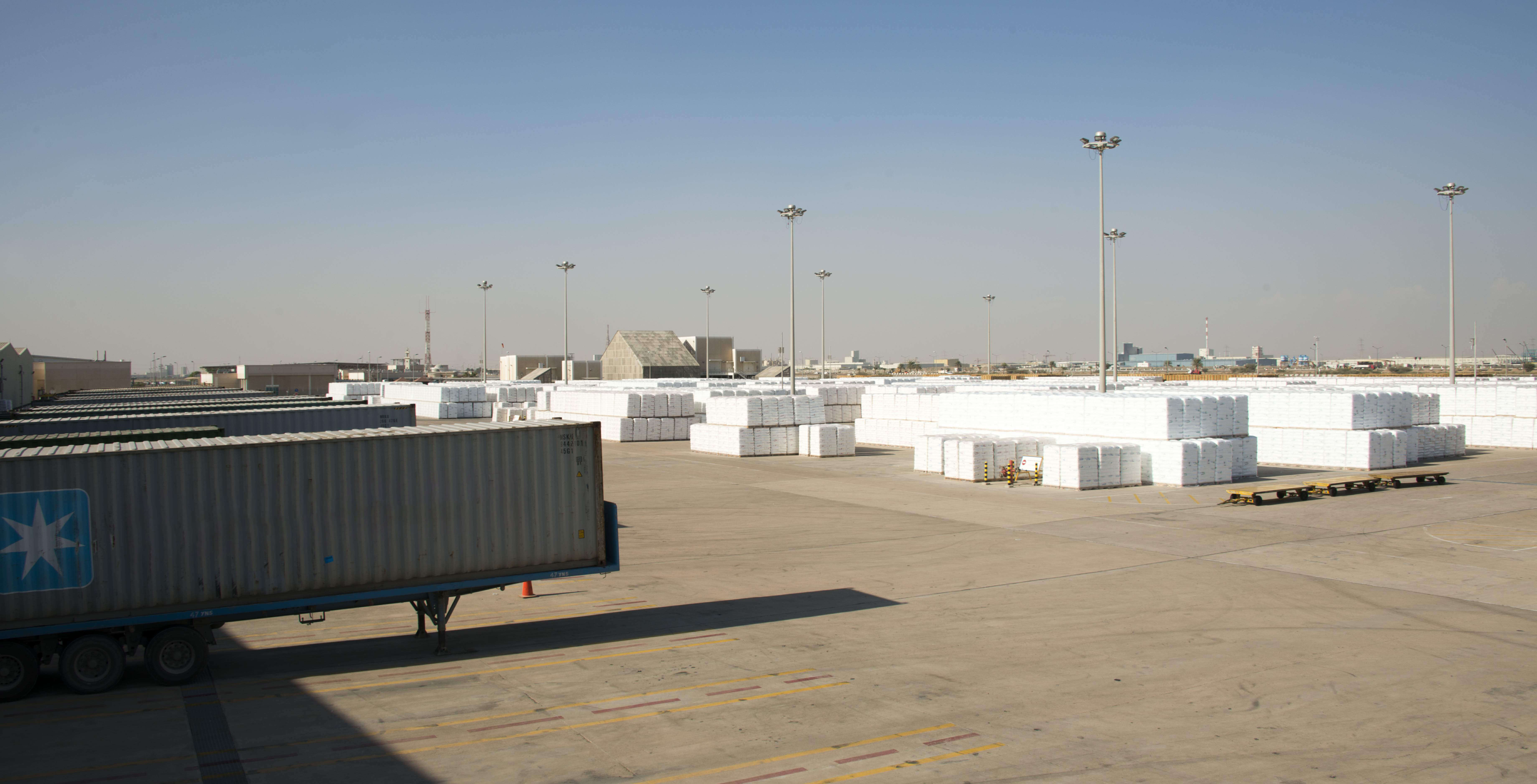
We have maintained a high level of reliability, agility and efficiencies delivering our products globally
OUTLOOK
Supply-chain disruptions continue to be the norm. This year has increasingly proven that static operating models no longer work. We will continue executing our strategy, proactively responding to market challenges while amplifying network resilience by diversifying the supply chain.
This includes leveraging the right capabilities with efficiency upturn and dynamism in the organization, reacting to challenges via a strong set of leadership skills combined with scalable situation management. It also means proactively responding to market challenges and disruptions to uphold business continuity at any given time.
We will continue leveraging our partnerships and collaborative investments to sustain our position in the era of New Norms and increasing competitive intensity. In this way, we will continue elevating our global network resilience to accommodate growth and manage sustainability developments while maintaining a strong focus on EHSS.
Digitalization is crucial to SABIC’s future supply-chain plans. We envision further enhancements by unlocking digital transformation to drive better supply-demand visibility and manage operational risk. This feeds into our plans to introduce a new operating model that improves service levels, lead times and cost effectiveness.
As the world transitions toward a more circular economy, we believe it is vital to move to greener supply chain, proactively engaging with authorities, regulators, and service providers. We aim to further achieve significant carbon-emission reductions to reach our sustainability goals.