MANUFACTURING CAPITAL
SABIC Corporate Manufacturing oversees all our plant operations at our sites worldwide. During 2022, working within constraints brought on by the fallout of the pandemic, the Ukraine conflict, and the fuel crisis, SABIC continued to focus on the execution of our global manufacturing strategy to achieve the highest levels of EHSS and operational excellence standards.
SABIC Manufacturing Strategy establishes a framework for accountability, ownership and realization targets, which enables us to mitigate risks, increase revenue, and optimize cost. The strategy comprises seven key strategic execution initiatives; Human Capital Development, Asset Lifecycle Management, CAPEX Discipline, Value Creation Leadership, Manufacturing Digitalization Programs, Risk Management and Operations Management System. Each initiative comprises a set of programs and targets (based on a 2022+4 Plan) and owners from both sides – corporate functions and sites. Progress reporting is based on an approved operating rhythm in which each action focal point reports on a quarterly basis and data is verified and published using a dedicated IT enabler. Data is later consolidated and shared during the quarterly manufacturing leadership meetings. Taken together, these mechanisms of strategy, execution and reporting form Manufacturing’s operational excellence vehicle, which drives SABIC’s progress toward its business plan and vision: “To be the preferred world leader in chemicals.”
In March every year, a workshop is conducted involving stakeholders from across SABIC’s business and functions to discuss manufacturing performance and identify “performance killers” hindering production plans. SABIC has developed and endorsed a five-year plan to address these performance killers with an anticipated production loss avoidance of 4.6 MMT by 2026. The overall implementation progress is at 48% with a total of 199 KMT and 123 production loss avoidance was realized. As a further outcome of the workshop, the Performance Killer Initiative was also extended to other paradigms, including production loss due to external reasons, such as feedstock limitations, technology limitations and project-related losses linked to Engineering and Project Management. Similarly, the concept of Asset Life Cycle (ALC) was extended to manufacturing sites. Within this concept, site-specific performance is analyzed and classified by the sites against the different ALCs to address encountered losses. Subsequently, the sites take specific actions to address these losses. This concept was included as an amendment to the manufacturing strategy KPIs, with site-specific targets for production-loss avoidance presented as a five-year plan.
ASSET MANAGEMENT AND PERFORMANCE
During 2022, SABIC launched the Integrated Asset Life Assessment iALAprogram to optimize the development of a bottom-up CAPEX investment portfolio for manufacturing assets. This program is designed to provide a robust and transparent framework to support assets-investment decision making for all manufacturing sites. This framework provides the processes and tools to consider costs, risks and performance to enable making better informed decisions that maximize the long-term value of ALCs. On the organizational side, the iALA framework establishes new rules of engagement between different SABIC organizations to promote cross-functional collaboration as a fundamental pillar to the generation of sound asset-investment decisions.
In the area of Asset Performance Index (APi), SABIC’s manufacturing sites have continued improvement in their manufacturing-excellence journey with a 2.4% improvement in APi over 2021 (75.5% to 77.9%). The APi measures our assets’ current performance, reliability, and integrity against 2025 manufacturing targets, considering both lagging and leading KPIs. Progress in this regard was made despite the introduction of new maturity programs to mitigate emerging asset risks related to underground piping, concrete cylinder pipelines and coating protection. (In general, new programs have low scores when first introduced, causing a drop in the leading KPIs and APi score. Nevertheless, improvement was made in other programs in 2022 to offset this drop). The stronger APi equates to a 1.4% increase in plant reliability.
This year, the asset-operations-discipline program finished its second self-evaluation cycle for Saudi based sites while commencing the first-cycle assessment for Europe and America sites. The program ensures that crucial operational components are implemented during production operations in an effort to further improve on our best-in-class standards while fostering an environment of empowerment within our manufacturing community.
Asset Performance Index (APi)
2021 |
|
2022 |
---|---|---|
75.5% | 77.9% |
SUSTAINABILITY THROUGH MANUFACTURING INNOVATION
Up-to-date technologies and technical solutions allow us to continuously fulfill sustainable practices. In 2022, we successfully designed and implemented an innovative real-time optimization technology at our olefins plants. This new solution has resulted in a significant value creation at two olefin crackers. Based on the success of this solution, a three-year program was developed to roll out this technology at the remaining crackers. The overall implementation progress of this program is at 35%.
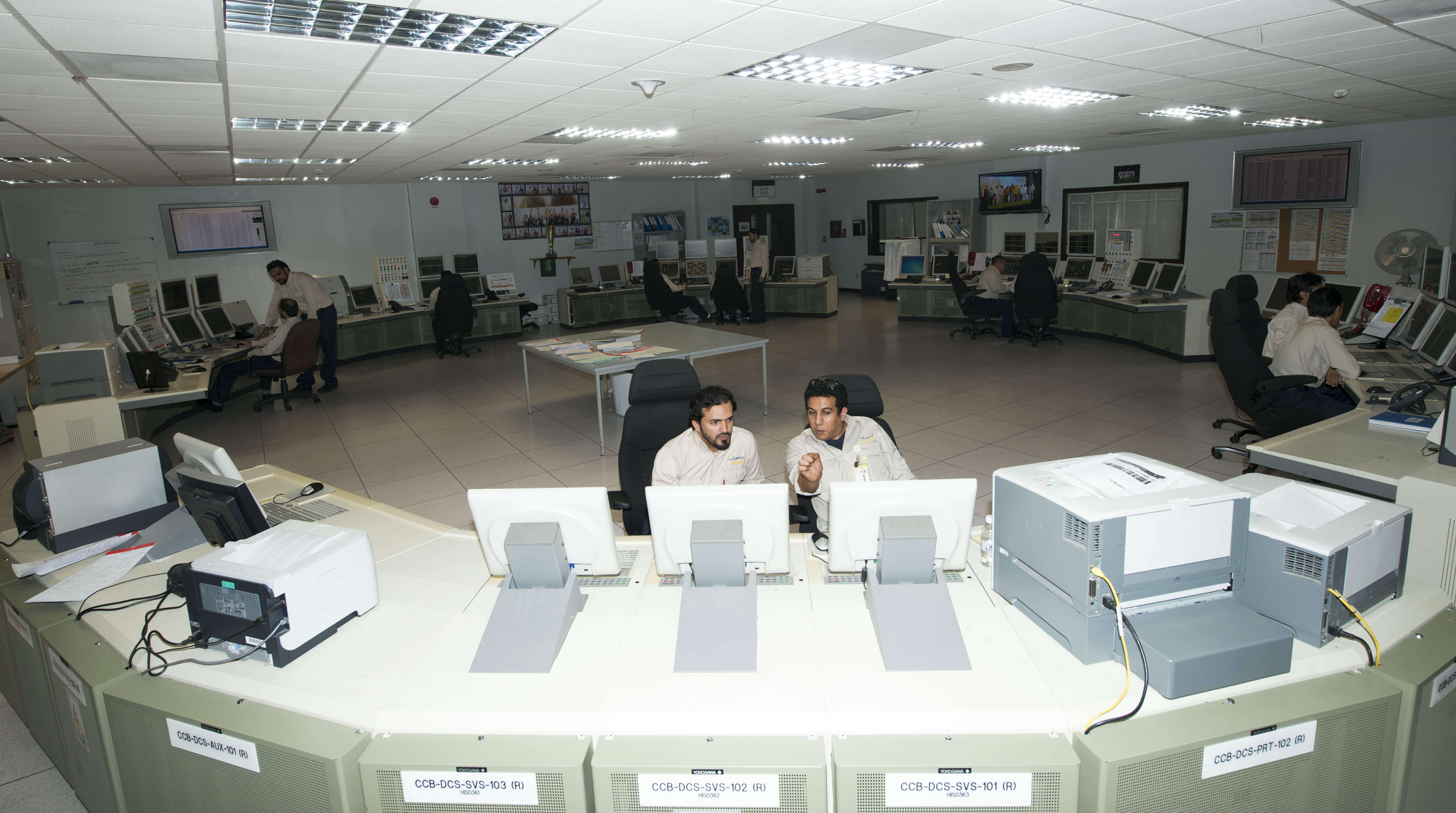
We create an inspiring work environment that forms the foundation of our people’s competitive performance.
OPERATIONS MANAGEMENT SYSTEM
During 2022, the Integrated Manufacturing Excellence Assessment (IMEA) initiative was introduced to assess the implementation of the Operations Management System (OMS) and Technical Programs. IMEA is a risk-based approach ensuring high risks are systematically identified and mitigated in operating units in all five OMS dimensions: people & organization, business performance & governance, EHSS management, ALC management, and continual improvements & quality management. The outcome is a sustainable improvement in all aspects of performance – that is, EHSS, culture, reliability, sustainability, quality, finance, etc. IMEA is now in its first cycle, and we expect to complete all SABIC manufacturing sites by the end of 2023.
WORKFORCE DEVELOPMENT
In manufacturing, we intend to practice the motto, “Be the Impact.” This is evident in the efforts exerted and the results attained by all sites globally this year. Our landmark Frontline Employees Development Program (Jadeer) continued to expand in scope and content to include three additional disciplines (inspection technicians, analyzer technicians and fire technicians), with major enhancements in security and cybersecurity competencies. Simultaneously, the SABIC Engineers early Development program (SEeD) and Technical Talent Development program sustained momentum with a special focus on improving employees’ experience and program structure. A new onboarding scheme was introduced and high-profile engagements and dialogue sessions were organized between SEeD employees and the manufacturing executive vice president and affiliate presidents. The new program structure was piloted at two Saudi-based sites (Petrokemya and Saudi Kayan) to help confirm program readiness for full-scale implementation.
We maintained efforts to embed the right leadership behaviors, with all sites working to complete action plans and close the gaps identified during the global virtual assessment of critical organization behaviors (COBs) as areas that need improvement. We achieved a completion rate that exceeded this year’s target of 80% as of Q3 2022. We are currently engaged in establishing a manufacturing learning center that integrates the technical talent-capability development programs under a single unified platform. We are focusing on synergizing this initiative with a number of human-capital development-optimization initiatives to ensure maximum value and impact.
We will continue to create a work environment that marks our human capital as the foundation of competitive performance, by inspiring and connecting them through our global networks, ensuring they are always motivated and challenged through diverse assignments, with access to excellent learning experiences and resources.
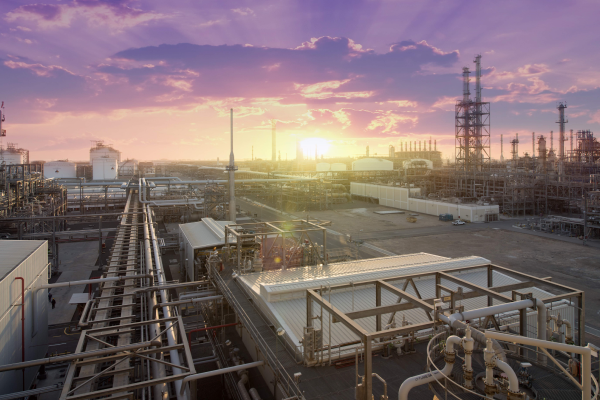
We focus on achieving the highest levels of operational excellence at our manufacturing plants.
ENVIRONMENT, HEALTH, SAFETY AND SECURITY (EHSS)
Protecting EHSS is a core component of our business.
The SABIC EHSS policy aims to meet all compliance obligations while instilling a mindset that thinks beyond compliance. As EHSS and regulatory compliance is one of the pillars that the SABIC 2025 manufacturing strategy has been built on, we proactively react to the continuous international regulatory developments concerning the environmental aspect, and constantly engage with national regulators and advocate for a balanced environmental/business framework that assures business continuity without compromising our surrounding environment.
As a member of Association of International Chemical Manufacturers (AICM) in the Asia Pacific region, SABIC joined in the regular workshops and participated in different external EHSS platforms to actively learn and understand EHSS regulation trends. We also took part in similar interactions across other regions, such as Europe (CEFIC and Plastics Europe) and the United States (via ACC).
As part of our key focus area of 2022, SABIC introduced a human failure model in eSHEM reporting and investigations to provide a better understanding of the type of human failure involved in such incidents.
This year, Leadership Engagement & Visibility workshops were held reaching more than 200 leaders. Multiple Safety, Health & Environment Management (SHEM) standard training sessions were conducted for the newly circulated SHEMs. Confined space simulators were constructed and introduced to three sites to allow training of various confined space scenarios. Furthermore, the KSA Safety Network initiated a taskforce team to drive improvements on basic safety behaviors like hand safety and avoidance of Slip-Trip-Fall incidents.
In 2022, SABIC EHSS Corporate also maintained certification in Responsible Care® 14001:2015, which included ISO 14001 at the corporate level and certification in ISO 45001:2018 in Saudi Arabia. We were able to assure conformity with the best international EHSS standards, achieve our EHSS objectives, and meet regulatory and contractual requirements.
Over the year, 123 candidates in different regions were successfully certified in our EHSS certification program. The program includes NEBOSH Diploma, NEBOSH International General Certificate in Occupational Health and Safety, BOHS (iCertOH) certification, and NEBOSH certificate in Environmental Management. In addition, 44 subject-matter experts were trained internally on Environmental Risk Assessment at the proficient level to enhance their competencies in risk discovery methods.
Regional crisis management teams conducted 15 site-based and region-wide exercises on responding to cybersecurity attacks coordinated by SABIC’s cybersecurity response team. Furthermore, we initiated the third enhancement phase for the Crisis Management Mobile Application used as a communication and announcement tool for all crisis teams globally.
GLOBAL SECURITY MANAGEMENT
SABIC has implemented an updated Security Risk Assessment (SRA) tool for small manufacturing sites. The new tool allows site security leaders to better identify threats to critical assets and implement appropriate risk response strategies. Training awareness sessions on use of the tool have been conducted in all regions.
New Security Maturity KPIs were introduced at SABIC sites this year. The KPIs indicate what audit action has been taken and specify the efficiency of the security systems. They reflect our current preparedness and functionality levels of the electronic security systems. The KPIs track the SRA recommendations to assist the leadership drive and monitor security management at SABIC manufacturing sites.
SABIC continued the development of security programs/initiatives including the development of security competency (Jadeer Site Security Program) for security guards in the MEA region.
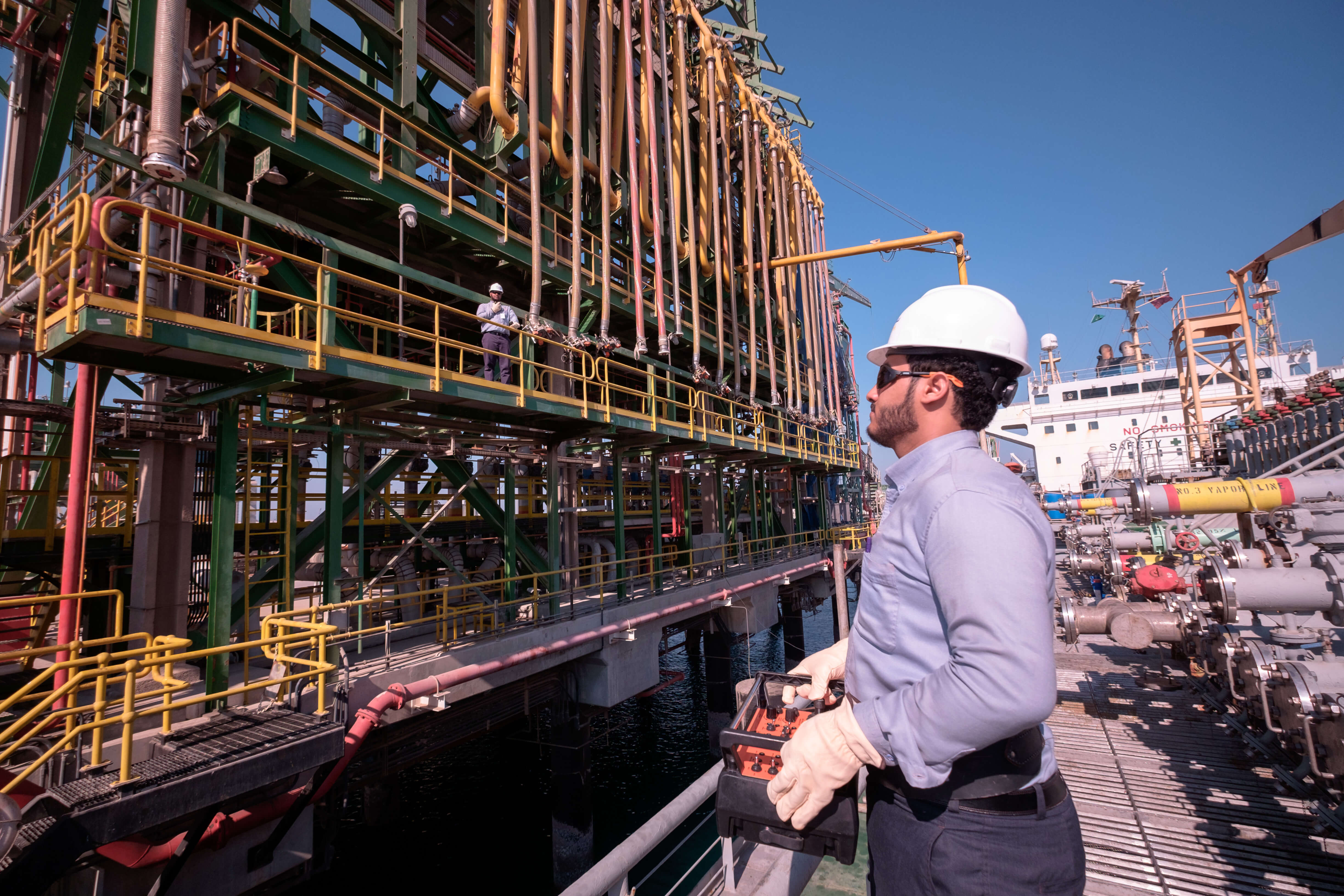
We work to cultivate a culture that strengthens health and safety competencies and policies across our organization
GLOBAL CRISIS MANAGEMENT
Regional and local crisis management teams continue to respond to the COVID-19 pandemic, weather-related emergencies and cybersecurity threats.
Cybersecurity remains an ongoing threat to the industry and has the potential to have a major impact on manufacturing operations. SABIC is committed to developing competency in its crisis-management teams to respond to all threats, including the threat of cybersecurity attacks. This year, the regional crisis management teams conducted site-based and region-wide exercises with an emphasis on response to cybersecurity incidents. Fifteen exercises were coordinated by SABIC’s cybersecurity response team. SABIC is committed to ensuring its crisis-management teams receive continuous training and crisis-management plans are updated.
SABIC initiated the third enhancement phase for the Crisis Management Mobile Application that is used as a communication and announcement tool for all crisis teams globally. Activities with IT were kicked off in Q4 2022, and the scope and blueprints were finalized, with go-live planned for Q1 2023.
PROCESS RISK MANAGEMENT
In sustaining the journey toward process-safety excellence, the global process risk management (PRM) function focused on its 2025 key strategic initiatives and improvement where needed.
PROCESS SAFETY COMPETENCY AND TRAINING DEVELOPMENT
PRM continued to build process safety competency across the entire organization by developing and offering relevant process safety qualifications and training programs throughout 2022. Incorporated within the SABIC process-safety-competency framework, each program follows the continuous improvement approach to both content and delivery. Process safety competency needs are also integrated into the OMS training matrix. We have worked to ensure continuity of key process-safety programs such as Process Safety Competency Development Program (PSCDP) for engineers, Process Hazard Analysis Leaders Qualification (PHALQ) Program and Foundations of Process Safety (FoPS) training. Further, PRM has initiated new learning interventions such as SOP-effective writing training delivered globally as well as piloted new training delivered by SABIC resources on explosion risk assessment & protection at the workplace.
RISK DISCOVERY AND MANAGEMENT
In keeping with our 2025 EHSS strategy, we focused on sustaining the mindset of welcomed risk discovery through smart KPIs. This mindset encourages staff to not only report risks but also respond with permanent mitigation measures through SABIC Assurance for EHSS Risk (SAFER) risk management and stewardship. With the global implementation of IT enabler (eSAFER), continuous monitoring and visibility for EHSS risks have been achieved, along with active IT-enabler enhancements to facilitate stewardship for EHSS risks.
As explosive dusts handling is a common process at several sites, a Dust Hazard Analysis (DHA) task was piloted in the MEA region along with training at sites that handle explosive dusts. DHA aims to ensure adequate understanding and assessment in handling explosive dusts to avoid dust-related explosions and fires.
In line with the continuous monitoring of incidents, PRM has developed a Loss of Primary Containment (LOPC) evaluation tool (incorporated in SABIC OMS) to support consistent classification of process safety events and drive informed decisions helping SABIC strive for learning and continuous improvement.
In addition to sustaining effective process-safety networking globally, PRM has expanded SABIC’s impact in the region through sponsoring regional process-safety conferences as well as active participation in the Gulf Petrochemicals and Chemicals Association’s newly formed process safety network reflecting SABIC’s responsible-care outlook.
EMERGENCY PREPAREDNESS AND RESPONSE CAPABILITIES
SABIC Emergency Response and Fire Protection focused its efforts on monitoring emergency response KPIs to improve our readiness for emergencies and the effectiveness of our response. In addition, we developed and arranged required competency programs and trainings for the emergency response team such as NFPA 1072- HAZMAT and Certified Fire Professional Specialist.
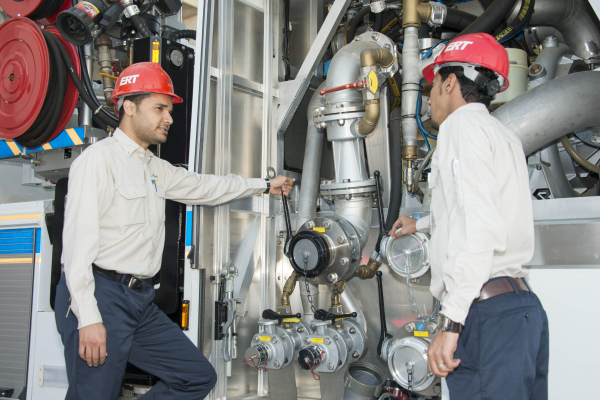
We monitor our emergency response KPIs to improve our readiness for emergencies